Simem Underground Solutions designs, engineers, and manufactures site-ready CRF/CAF, Paste Backfill, Shotcrete, and Grout plants with pumping systems for on-surface and underground mining, tunnelling, infrastructure and heavy construction projects worldwide.
Trusted Solutions with Proven Results
Simem Underground Solutions specializes in the global design and supply of cemented aggregate backfill and pastefill plants, slurry and bi-component grout plants, long distance pumping systems, and fully-automated material handling solutions.
Based in Abbotsford, British Columbia, Simem Underground Solutions has assembled a top-flight team of industry-skilled engineers and designers to deliver unquestioned solutions for the tunnelling and mining community. This broad group of experienced professionals possess expertise ranging from project specific equipment design, to operator training, installation commissioning, technical support, and spare parts service.
Tunnelling Solutions
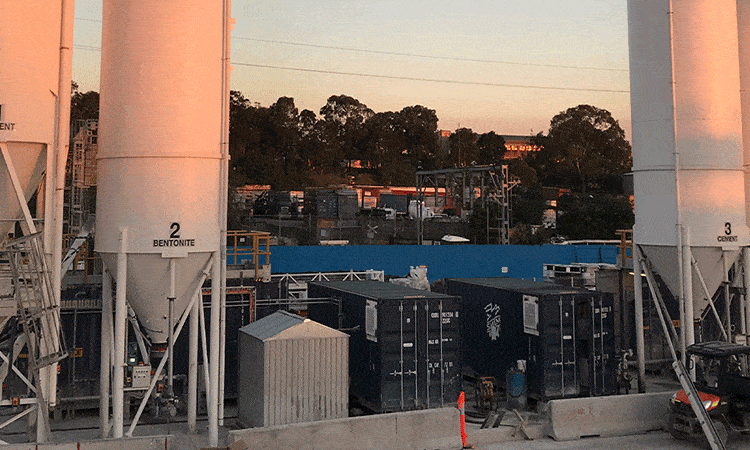
Approaching 1,600 km of Tunnelling
Featuring fully-automated high-shear colloidal mixers, our bi-component grout, cellular concrete, and bentonite mixing plants offer unsurpassed mixing quality with reduced labor requirements and measurable raw material savings. Globally renowned for their high quality and durable reliability, our products are recognized by customers as a mission-critical necessity to ensure project success.
Mining Solutions
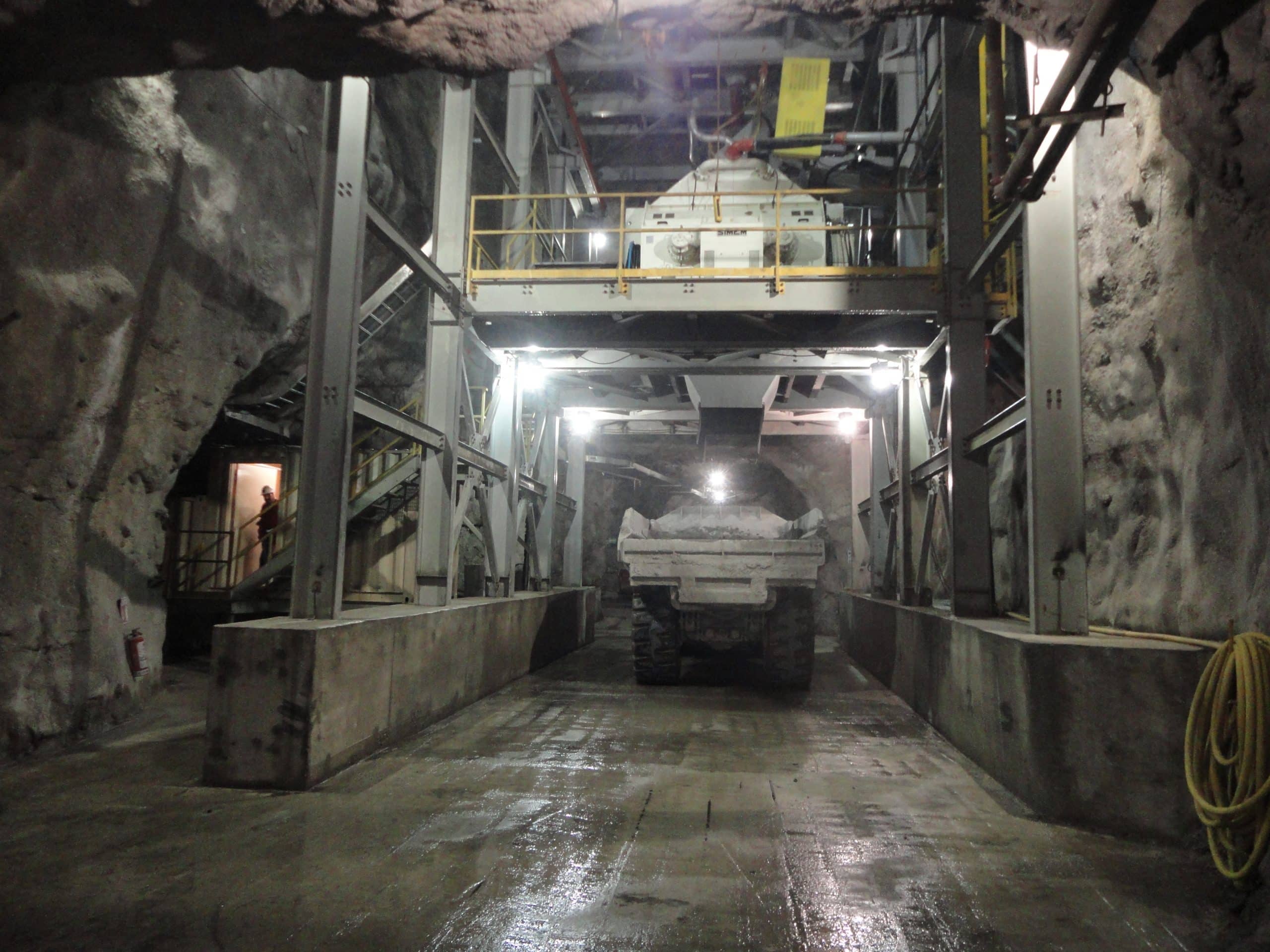
Over 100 Million Tonnes of Backfill Produced
With decades of mining experience, our dedicated team of engineers and designers provide custom backfilling solutions for the global marketplace. For projects requiring a fixed pastefill plant on surface, or a semi-mobile cemented rockfill plant underground, a complete solution from initial concept through final commissioning can be delivered.